How do you choose a pressure gauge?
To properly select a pressure gauge, you will need to consider the pressure gauge dial size, pressure measuring range (scale range), casing material, process connection, connection location, and more.
All these common specifications are crucial. However, the complexity often requires users to spend considerable time researching to find the perfect gauge.
With over two decades in Taiwan’s precision instrument industry, SJ Gauge can help. We have compiled seven key points to guide you in purchasing a proper pressure gauge. You can also directly contact us. Our professional team at SJ Gauge is ready to provide customized pressure or temperature measurement solutions at any time.
#01Dial Size of Pressure Gauges:
How to choose the right pressure gauge dial?
The dial size is related to the observation distance and readability. The farther the pressure gauge is from the observer, the larger the dial size needed. In actual practice, the selection standard is based on the readability of the user (convenient observation). Commonly used dial sizes are:
- 1.5" (1 ½" or 40mm)
- 2" (50mm)
- 2.5" (2 ½" or 63mm)
- 3" (75mm)
- 4" (100mm)
- 6" (150mm)
- 8" (200mm)
- 10" (250mm)
#02Scale Range of Pressure Gauges:
How does the pressure measurement range affect the selection of a pressure gauge?
To ensure safety during pressure gauge measurements and extend the gauge's lifespan, it is common to select gauges with dials that cover the commonly used pressure range between 25% to 75% of the scale (as shown in the diagram below).
For example, if the commonly used pressure and maximum pressure range from 2.5 kg/cm2 to 7.5 kg/cm2, it is recommended to purchase a pressure gauge with a dial scale ranging from 0 kg/cm2 to 10 kg/cm2. Choosing a pressure range that is too large may hinder observation (if the yellow area in the diagram is too large), while a range that is too small may pose risks of overpressure and bursting (if the red area in the diagram is too small), potentially leading to damage to the pressure gauge. Commonly used units include bar, psi, MPa, and kgf/cm2 (often abbreviated as kg or kg/cm2).
#03Case Material of Pressure Gauges:
How important is the material of the casing when purchasing a pressure gauge?
The material of the pressure gauge casing is crucial as it refers to the material surrounding the dial. This material needs to withstand environmental conditions and should not be susceptible to corrosion, melting, or condensation that could affect the accuracy of the pressure gauge.
Therefore, before selecting the appropriate material for the pressure gauge casing, it is essential to determine which environmental conditions are relevant for your industry or machinery. Considerations for environmental conditions include temperature, airborne particles, condensation, humidity, water vapor, and chemical substances, all of which can impact the performance of the instrument.
For instance, if your application requires the pressure gauge to be submerged in liquid or exposed to extremely humid environments, it is advisable to choose a gauge with a waterproof or well-sealed casing material. Stainless steel casing pressure gauges are recommended in such cases to prevent condensation or corrosion of the instrument. On the other hand, for many indoor industrial applications not exposed to direct sunlight or extreme weather conditions, a standard black casing pressure gauge may suffice.

Material | Characteristic |
---|---|
Black painted-iron | • More economical • Not acid or alkali-resistant. • Not suitable for outdoor environments as it is not water-resistant, causing malfunctions |
Stainless Steel | • Resistance to corrosion, weak acids, alkali, and water • Suitable for outdoor environments • Two categories: 304 SS and 316 SS |
Phenolic | • Commonly used in environments at risk of sea breeze erosion |
#04Liquid-Filled or No Liquid Pressure Gauges:
Liquid-filled pressure gauges are suitable for environments prone to pulsation (measuring unstable media) and vibration (generated during equipment operation).
Liquid filling prevents the pointer from being affected by vibrations, ensuring accurate readings, and also lubricates the gears on the dial to extend the gauge lifespan. Typically, glycerin is used as the filling liquid, but in specific cases, silicone oil may be employed.
However, liquid-filled pressure gauges carry the risk of liquid leakage. Therefore, if such conditions are not present, non-liquid-filled pressure gauges might be preferable.
#05Connection Location of Pressure Gauges:
Pressure gauges can be primarily classified into two types: lower mount and back mount. The lower mount type is also known as the "bottom mount".
To ensure easy readability for the observing personnel, it is essential to examine the pressure gauge type (looking at the installation method) and ensure its suitability for the specific application.
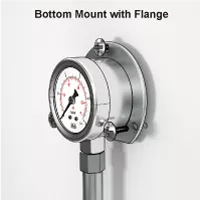
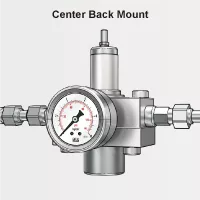
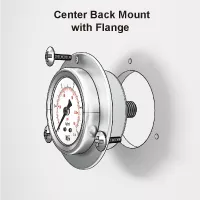
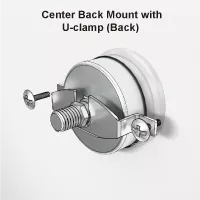
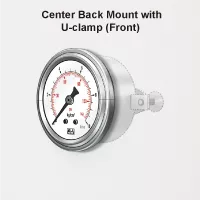
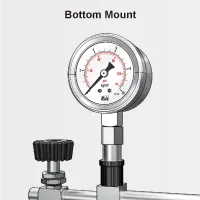
#06Process Connection of Pressure Gauges:
By clamping the vernier caliper around the threads, the diameter can be measured. The pressure gauge's threads can be categorized into straight threads (also known as parallel threads) and tapered threads (also known as conical threads).
Pressure gauge connections commonly used in European countries and industrial applications are referred to as British Standard Pipe (BSP). In North American countries, the American National Pipe Thread (NPT) is more commonly used.
For more detailed thread specifications, please refer to the brief The Introduction and Selection of Common Connection Specifications.
#07Wetted Part of Pressure Gauges:
The wetted parts of the pressure gauge, including the Bourdon tube and socket, must be compatible with the medium being measured. If the medium is incompatible with the wetted parts of the pressure gauge, it can cause corrosion and lead to pressure gauge failure, ultimately resulting in safety issues.
The blue area in the following image represents the wetted part of the pressure gauge. Common materials for these parts are copper and stainless steel. Copper is budget-friendly but relatively less resistant to corrosion and acids. For corrosion and acid resistance, 304 stainless steel or 316 stainless steel can be used. When measuring dense, highly corrosive, or impure media, it is recommended to use a diaphragm pressure gauge.
There are numerous possibilities concerning the compatibility between the pressure gauge connection and the measured medium. We will delve into these topics in-depth in our future discussions.
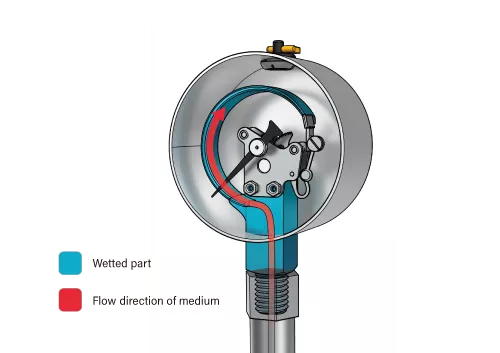
Further Information
In addition to the seven key points when choosing a pressure gauge, it is also important to consider calibration, accuracy testing, and quality inspection before shipment. As a trusted Taiwanese industrial instrumentation expert, SJ Gauge provides pre-shipment calibration, testing, and product quality inspection reports to ensure excellent product quality that meets your customized requirements.SJ Gauge offers tailor-made measurement solutions to oversee every step of your pressure gauge procurement process. Whether it's selecting the right specifications, assembling components, calibration, or regular maintenance, we are dedicated to providing you with outstanding products and support. Click to contact us and let SJ Gauge deliver the best customized measurement solutions for your industry applications.
Credit and Reference:
ASME B40.100-2022: Pressure Gauges And Gauge AttachmentsASME B40.100-2022
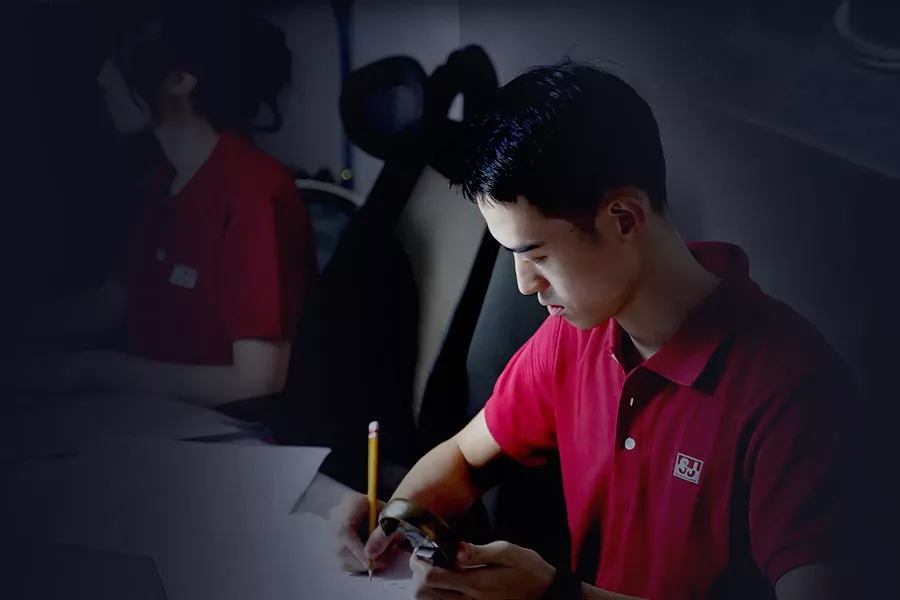
In addition to the seven key points when choosing a pressure gauge, it is also important to consider calibration, accuracy testing, and quality inspection before shipment. As a trusted Taiwanese industrial instrumentation expert, SJ Gauge provides pre-shipment calibration, testing, and product quality inspection reports to ensure excellent product quality that meets your customized requirements.
SJ Gauge offers tailor-made measurement solutions to oversee every step of your pressure gauge procurement process. Whether it's selecting the right specifications, assembling components, calibration, or regular maintenance, we are dedicated to providing you with outstanding products and support. Click to contact us and let SJ Gauge deliver the best-customized measurement solutions for your industry applications.